Production Planning & Scheduling
Optimize Your Planning Decisions
Four enablers for accelerated production planning & scheduling
Manufacturing companies that intend to lead the way in digitizing their planning and scheduling efforts and want to make a lasting impact with AI have to overcome some organizational and technical challenges. Happily, technology is rapidly evolving, and new platforms and tools are coming on the market that provide the necessary technical building blocks to address these challenges and make it possible to embed analytics in every aspect of the day-to-day or even minute-to-minute decision making processes.
In a series of blog posts we show what it takes to successfully implement a digitized production planning and scheduling process at scale. We identified four key enablers that will help planners in making better, faster, and smarter decisions. Previously, we discussed the value of building a digital twin from a planners perspective, why it's worth digitizing all planners knowledge and how to digitize your way of working. In this post we look at how to optimize your planning decisions with advanced analytics.
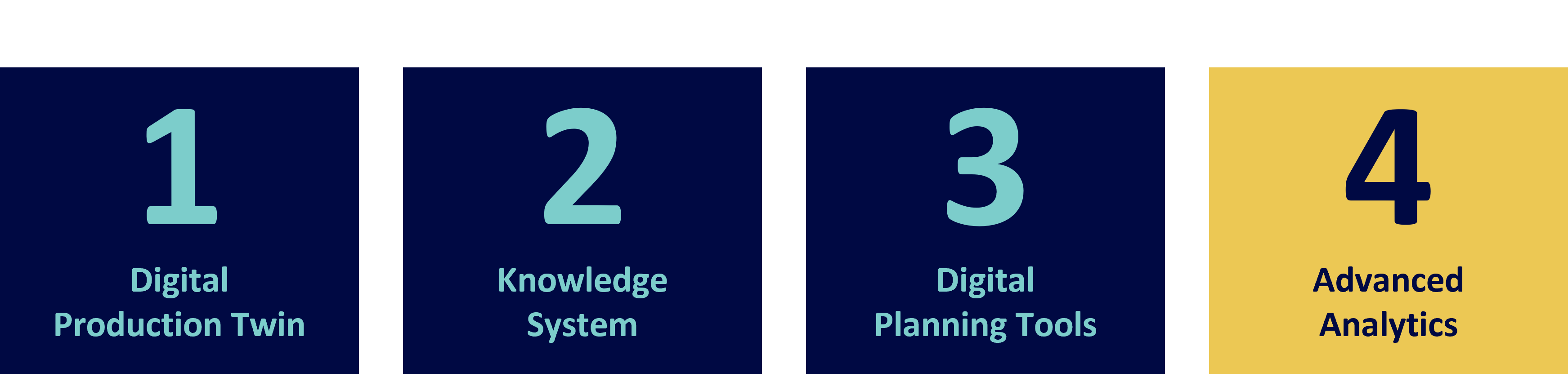
Four enablers for accelerated production planning & scheduling - step 4
No need to write or understand code
Production planners are typically not mathematicians or programmers. Nevertheless, data and analytics are the key accelerators of an organization’s digitization and transformation effort, and the benefits for production planning and scheduling are clear. Advanced analytics can assist planners in tackling planning problems too difficult to grasp for the human mind and propose solutions in line with enterprise-level objectives to maximize operational efficiency.
It might be a good idea to add some data scientists to the team, but finding data professionals who both understand the complexities of an industrial production environment and are able to collaborate with production and supply teams on a daily operational basis are very hard to find.
Low-code solutions make complex analytics available for production planners.
Fortunately, a new generation of low-code tools is emerging to make complex analytics and state-of the-art optimization algorithms accessible for the everyday business user, without the need to write or even understand code.
Optimize your decisions, balancing multiple objectives
Leveraging AI to determine the most optimal production strategy in any given situation will give a significant competitive advantage to the company that adopts it.
Production schedules can be generated in line with the specific challenges and constraints of each planning cycle, balancing multiple objectives:
- On-time Delivery: how many orders or commercial value in a pool of orders competing for the same resources and assets can be (partially) fulfilled? What part of those produced orders will be ready in time and which service level can be guaranteed?
- Capacity Utilization: how much capacity is being used from the total available capacity of all machinery and resources needed to produce goods? Is the factory operating at or near full capacity and to what degree can capacities being stretched?
- Delivery Reliability: how accurate is a production schedule? Capacity utilization will not be stretched to the limits and asset reliability – when available - should be taken into account when delivery reliability is key. Producing orders just before due date will be avoided to ensure products can be delivered as promised.
- Production run-time: how long does it take to produce a group of orders? This is especially important when the production sequence of orders has a large impact on the total make-span. Product switchovers will be minimized to reduce idle time and boost production efficiency.
- Product Quality: how likely is it that goods will be produced with acceptable and consistent quality? Shorter production runs with frequent switchovers can result in quality problems. Also, high value products or critical orders should not be scheduled on less reliable assets when product quality is important.
- Overall Equipment Effectiveness (OEE): how to maximize manufacturing effectiveness through a fully optimized production schedule? Extend the equation with maintenance activities and asset health indicators next to all production requirements to decrease overall downtime and boost production output.
Want to know more?Download our whitepaper on how to accelerate with production planning & scheduling.